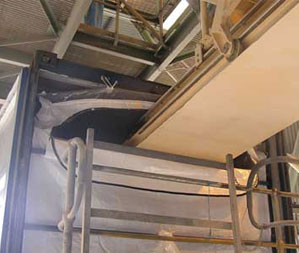
JMP Holdings is one of New Zealand’s top suppliers of ISO bulk container liners. Our clients across the nation enjoy the huge benefits of transporting free-flowing bulk materials by land and sea in polyethylene liners.
JMP Container Liners protect products from contamination and the environment from product pollution. Products are kept secure, clean and dry by enclosing them within their own disposable shell – and with no end clean up of the container necessary, saving product, time and money. JMP Container Liners are designed and tailored to meet client’s precise individual requirements and ensure fast, controlled loading and unloading by a wide range of systems.
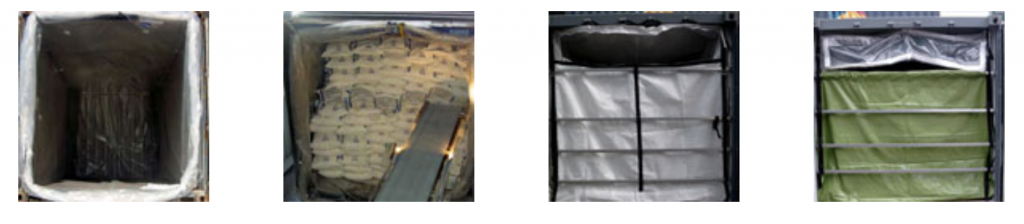
All JMP Container Liners are quality assured and manufactured in clean conditions from strong, durable, food grade polyethylene. Extensive development of both products and manufacture ensures the very highest levels of performance and reliability. JMP Container Liners control and protect a vast range of bulk chemicals and foods whilst offering savings of as much as 80% of the costs of handling them by other means – not surprising our clients include many of the world’s leading producers, transporters and operators.
WHY USE CONTAINER LINERS?
- Protects products from contamination
- Seals out water
- Fast to install, load and discharge
- Tailored to all filling and discharging systems
- Highest quality performance and reliability
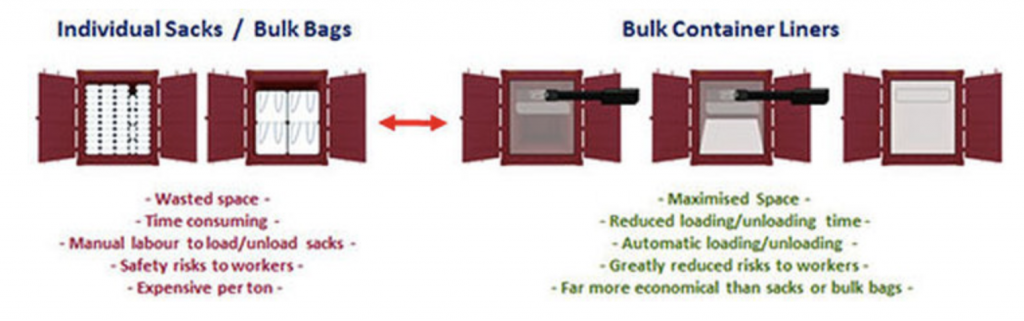
HOW ARE CONTAINER LINERS USED?
Container Liners are suspended inside the container and can be air or inert gas inflated if required. Loading can be by gravity from overhead hoppers through top fill hatches or through the doors and a false bulkhead using screw or belt conveyors, paddle or belt throwers or a variety of pneumatic systems.
JMP Container Liners can be fitted with any combination of top or end fill/discharge spouts correctly aligned with hatches in the container or apertures in false bulkheads or have a completely open end to allow fork lift truck access. They can have fabric end facings which, when combined with rigid bars, act as a false bulkhead and which can have a zipped, wide mouth filling opening.
After loading, spouts are detached from the filler, folded and sealed. Wide mouth openings are closed by means of a zip in the fabric front. Fork-lift truck “drive-in” liners are extended to allow the opening to be tied closed. Once the liner is closed, the product is completely insulated from the environment and protected from contamination. Unloading is determined by the equipment in use at the product’s destination.
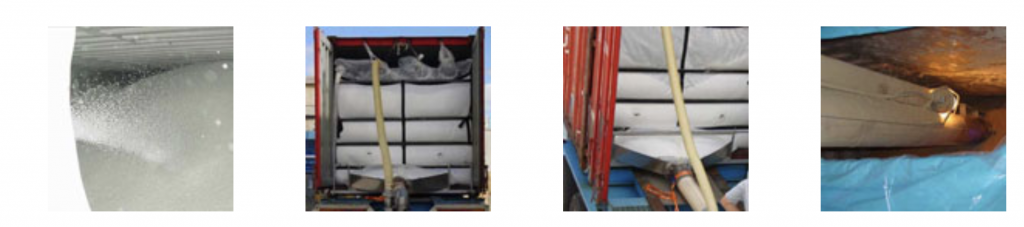
Containers are discharged by tipping them either by means of a tipping chassis on the delivery vehicle or a tipping platform which may tilt the whole vehicle or the container alone. When a completely sealed discharged system is required, as for sensitive chemicals, a spout is incorporated into the end of the container liner which can be tubular or triangular and which is sealed to a rotary valve. This directs the products into a pneumatic conveying system which carries it up into a silo. If the product is dusty, a ventilation tube can be incorporated into the liner which is connected to the exhaust of the rotary valve and recycles the dust particles back into the liner. Some products are discharged simply by cutting the end of the liner over a grating. Once discharging is complete, the liner is removed leaving the container clean, dry and ready for another load.
TYPICAL CONTAINER LINER AND BULKHEAD SYSTEMS
Whatever filling and discharging systems you have in place, we can provide a Container Liner to suit. Shown below, are some of our most popular configurations.
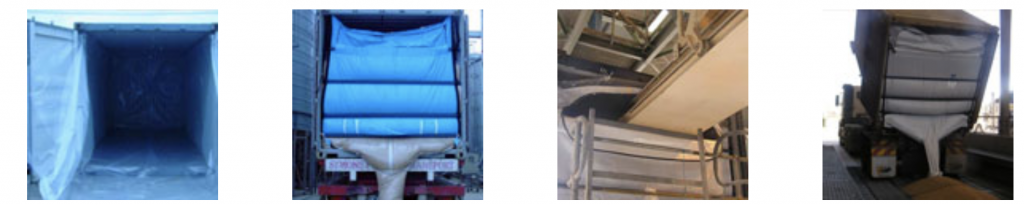
CONTAINER LINER APPLICATIONS
Liners are used for a wide and constantly growing range of granular and powder products as a highly effective and time saving alternative to sacks and bags. The following is merely an illustration of some of the products suitable for transportation in liners:
CHEMICALS – Click on each product to view the most suitable liner
If you have any questions regarding our Bulk Container Liners please contact us.
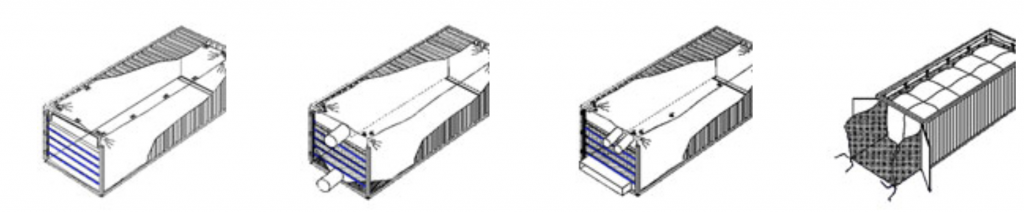